A research team from the Chair of Production Engineering of E-Mobility Components (PEM) at RWTH Aachen University has conducted a comparative analysis of Tesla and BYD’s traction batteries, uncovering notable differences in design and efficiency. The study involved dismantling current batteries from both manufacturers to evaluate various aspects, revealing “surprising results” with previously undocumented data.
Professor Achim Kampker, Director of PEM, highlighted the motivation behind the research, stating, “Both players have only ever revealed little data about their batteries, so the cells’ mechanical structure and most of their properties have remained hidden to date.” This scarcity of detailed information prompted the team to undertake a thorough examination of the latest electric vehicle (EV) batteries from Tesla and BYD.
Published on March 6 in the journal Cell Reports Physical Science (full study), the findings indicate that Tesla’s 4680 cells are designed with a focus on high energy density, whereas BYD’s blade cells prioritize volume efficiency and the use of more cost-effective materials. The study concluded that BYD’s battery is more efficient due to its simpler thermal management system.
The researchers analyzed the mechanical construction, dimensions, electrical and thermal properties, and material composition of the electrodes in both batteries. Additionally, they assessed the costs associated with cell materials and assembly processes. Tesla’s cells were obtained from Munro & Associates following the teardown of a 2022 Tesla Model Y, while the BYD Blade cells were sourced online from a Chinese dealer and verified to have a State of Health (SoH) of 100%.
Overview of general cell properties and dimensions | ||
---|---|---|
Property | Tesla 4680 cell | BYD Blade cell |
Nominal capacity, Ah | 23.125 | 135 |
Nominal energy, Wh | 85.56 | 432 |
Nominal voltage, V | 3.7 | 3.2 |
Voltage window, V | 2.5–4.3 | 2.6–3.65 |
Weight | 355 g | 2.7 ± 0.3 kg |
Volume, mL | 133 | 1,216 |
Energy density (gravimetric), Wh/kg | 241.01 | 160 |
Energy density (volumetric), Wh/l | 643.3 | 355.263 |
The areal capacity of the cathode (calculated), mAh/cm² | 4.99 | 2.393 |
Dimensions | ||
Property | Tesla 4680 cell | BYD Blade cell |
Diameter/length, mm | 46 | 965 |
Height, mm | 80 | 90 |
Thickness, mm | – | 14 mm |
Can wall thickness (sides), mm | 0.4 | 0.3 |
Separator, μm | 10 | 12 |
Anode coating thickness, μm | 125 | 65 |
Copper substrate foil thickness, μm | 10 | 10 |
Cathode coating thickness, μm | 75 | 70 |
Aluminum substrate foil thickness, μm | 20 | 20 |
No. of separator layers | 2 | 78 |
No. of cathode sheets (coating on both sides) | 1 | 38 |
No. of anode sheets (coating on both sides) | 1 | 39 |
One significant discovery was the absence of silicon in the anodes of both batteries, a material typically used to enhance energy density. The energy density measurements revealed that BYD’s LFP cells achieved 160 Wh/kg and 355.26 Wh/l, compared to Tesla’s 4680 cylindrical cells with NMC811 chemistry, which reached 241.01 Wh/kg and 643.3 Wh/l. This difference demonstrates Tesla’s emphasis on volumetric energy density.
In terms of form factor, BYD’s blade cells are long and prismatic, measuring 90 mm in height, 14 mm in width, and 965 mm in length. Tesla’s cylindrical cells have grown in size from the smaller 18650 format to the larger 4680 cells, enhancing energy content and simplifying system integration. Both manufacturers utilize laser welding for joining thin electrode foils, an unconventional assembly method.
The study also highlighted differences in safety design and electrical contact systems. Tesla’s 4680 cells are installed upright to allow security vents to function downward during emergencies, while BYD’s cells vent to the side. Additionally, Tesla uses the entire cell container as the negative pole, whereas BYD insulates both poles from the housing.
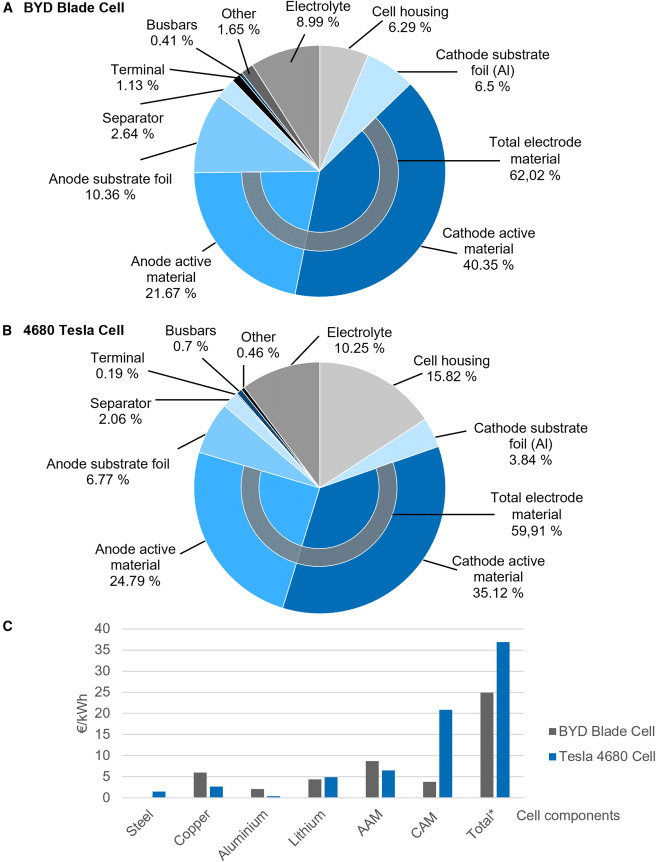
Cost analysis revealed that BYD’s cells are approximately ten euros cheaper per kilowatt-hour, primarily due to differences in cathode materials and container composition. Supported by Münster Electrochemical Energy Technology (MEET) and the Fraunhofer Institute for Ceramic Technologies and Systems (IKTS), the study is available for free download and includes further analysis on electrode arrangements and contacting methods.